The DIY Pick and Place machine upgrade to use automotive vacuum valves didn’t work as planned as the automotive valves are much too slow and unresponsive to switch the vacuum feed to the picker needles fast enough to pick and place the components.
We replaced the old solenoid valves as they had a very restricted airflow due to a very small valve port inside the units.
The valves had an aperture of approx. 1mm with a small rubber seal and this was causing the vacuum to the needles to be very restricted, especially on the 2.5mm needle for picking chips from the vibration feeder.
We initially enlarged the valve port to 1.5mm and found this was working without any problems so we then used a 2.5mm drill to take the valve port to the limits of the material available on the valve seat which has made a huge difference in the suction available on the picker needles.
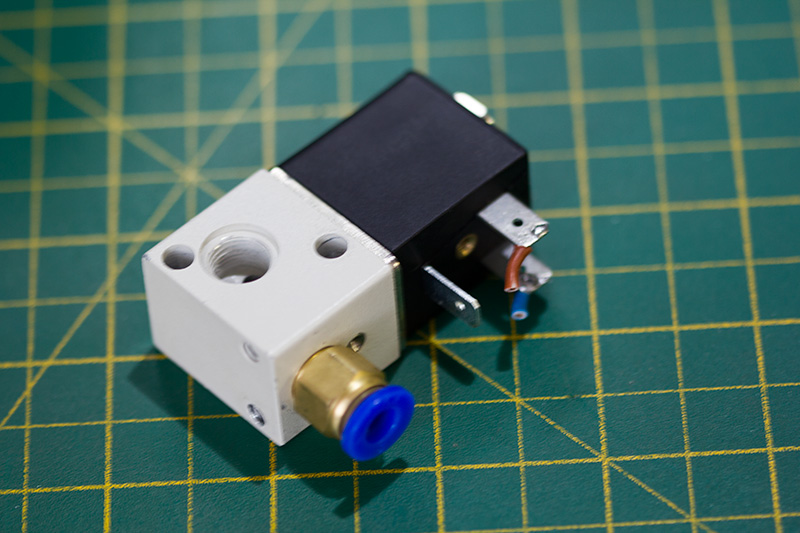
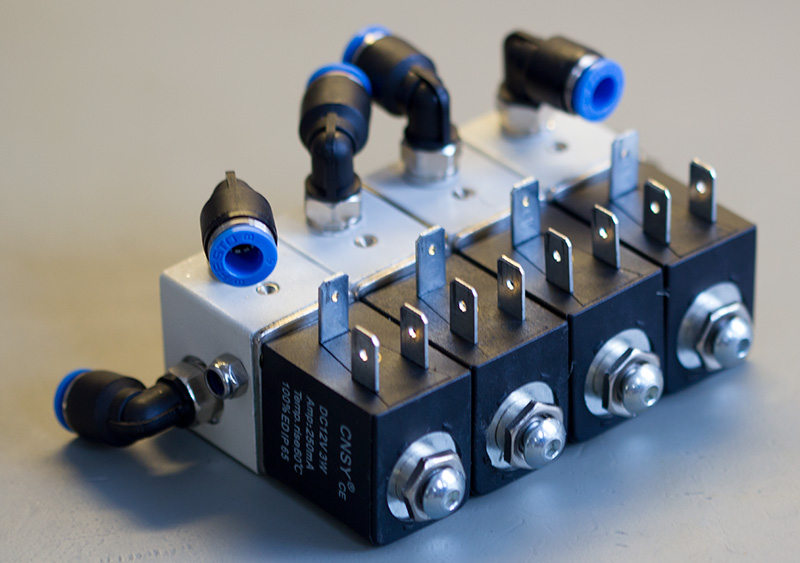
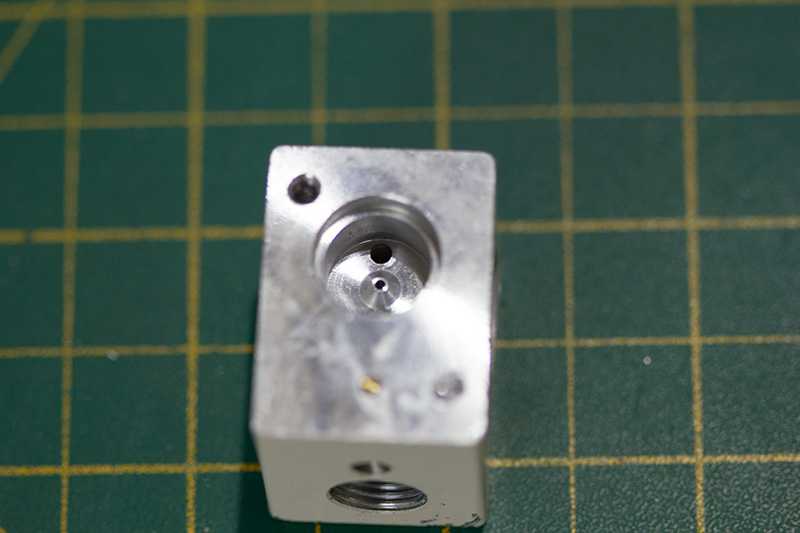
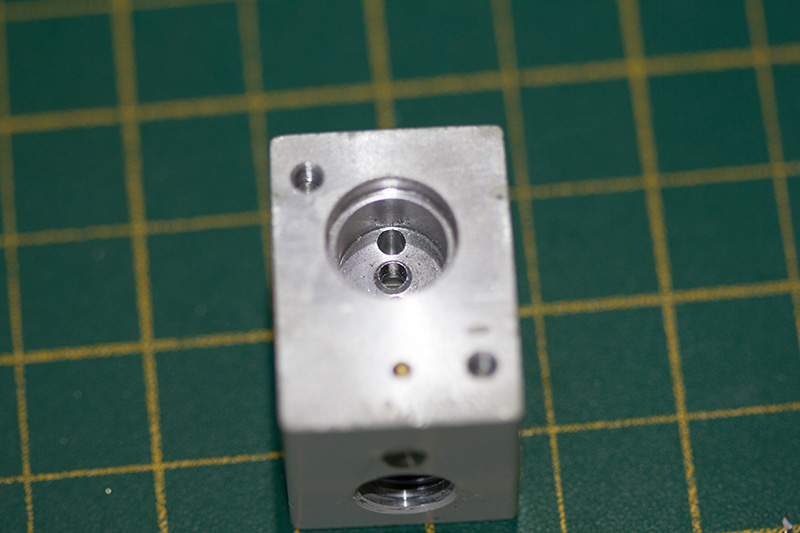
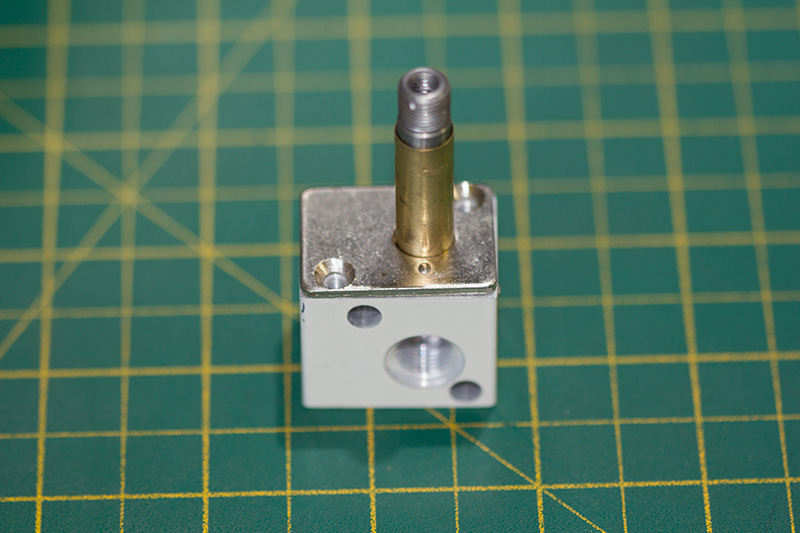
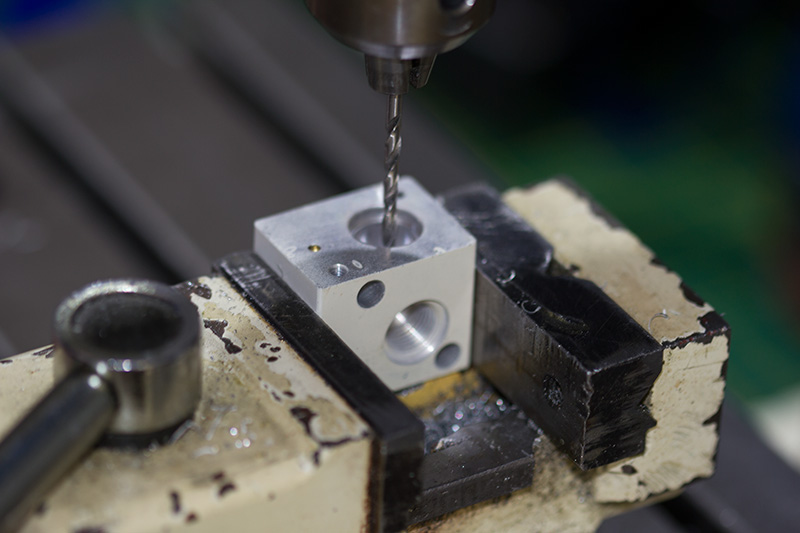
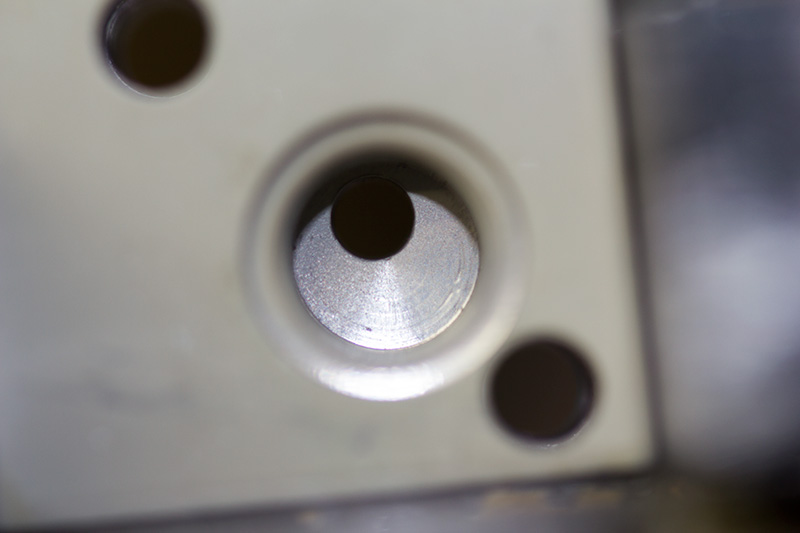
Now we have resolved the issues with the limited vacuum on the pickers, we need to design and build a system to provide a small “puff” of air to dislodge the component from the picker’s needles when placing each part on the PCBs when the vacuum is turned off.
Comments