In July 2014 we modified the vacuum valves to try to improve the air flow to the picker nozzles by drilling the aperture to a larger diameter. This initially worked but the valve seat wasn’t making a very good seal after they had been used for a couple of months and this resulted in some components moving and not placing correctly.
We took the decision to abandon the cheap eBay Chinese valves and go with professional grade vacuum and compressed air valves from SMC.
Our plans to make an “air puffer” to provide a small pulse of air to release the component using a speaker and a sealed enclosure turned out to not work as well as we had hoped and so we decided to change the way the control board switches the solenoid valves and drive the new valves from the 24 volt supply and switch this using the GPIO header we had included on the control board rather than using the on-board 12 volt solenoid controllers which toggled between the air and vacuum supplies for each picker nozzle.
We made a simple single sided PCB to run the four new solenoid’s and this uses a darlington transistor for each output which is driven via a current limiting resistor on the GPIO port from the main controller.
Using the new driver board we can now control each solenoid valve independently with a dedicated vacuum valve and a compressed air valve supplied with low pressure air via a regulator to give a very short “puff” of air to dislodge the component when it is placed.
For the new valves we did a lot of online research for the various types of valves available and after discussing our requirements with Chris at pneu-store who was very helpful, we ordered a pair of vacuum valves model SMC VDW24WA (Download datasheet PDF) which have a 3.2mm orifice and 1/8 inch port size from their online store at www.pneu-store.co.uk which arrived a few days later along with a big catalogue of their other components.
For the compressed air valves we ordered a pair of SMC VT307 G 1/8 3/2 Solenoid valves (Download datasheet PDF) from RS Components.
We mounted the new valves on an offcut of acrylic clear sheet and using 1/8 push fit fittings we setup the valves with a shared air and vacuum supply and “T” connectors between the outputs to go to each picker nozzle.
One problem we have found in the past was that small components sometimes got sucked up the vacuum pipes and made their way into the pump and valves which may have been the cause of the valve seat failure before. To resolve this problem we made two small inline vacuum filters using a small section of clear acrylic tube which we threaded with a 1/8 BSP thread on each end and then using a piece of fine metal mesh we made small filters over the end of a pencil which were fitted into one of the push fit connectors which had been screwed into the clear tube.
The new filters will now allow us to see any components have been picked up incorrectly and sucked into the system and stop them from reaching the valves and causing further damage.
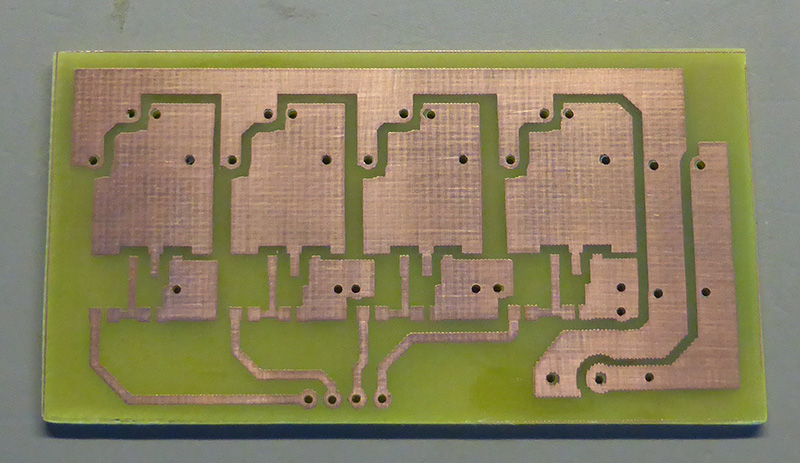
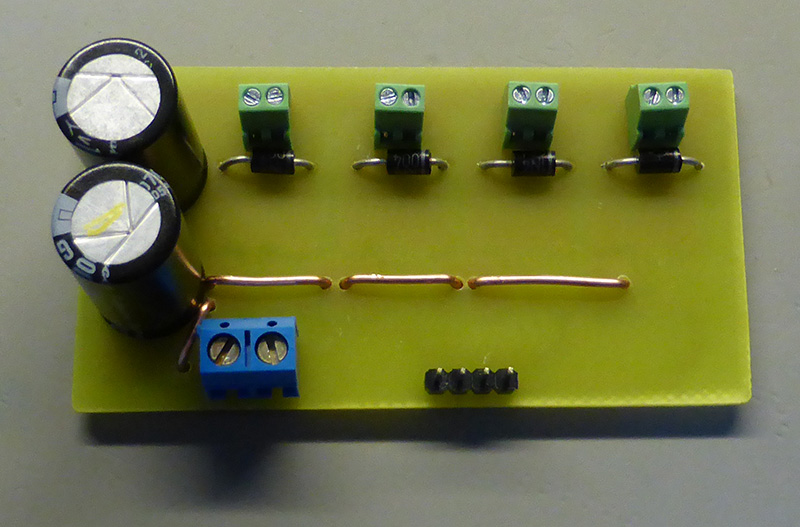
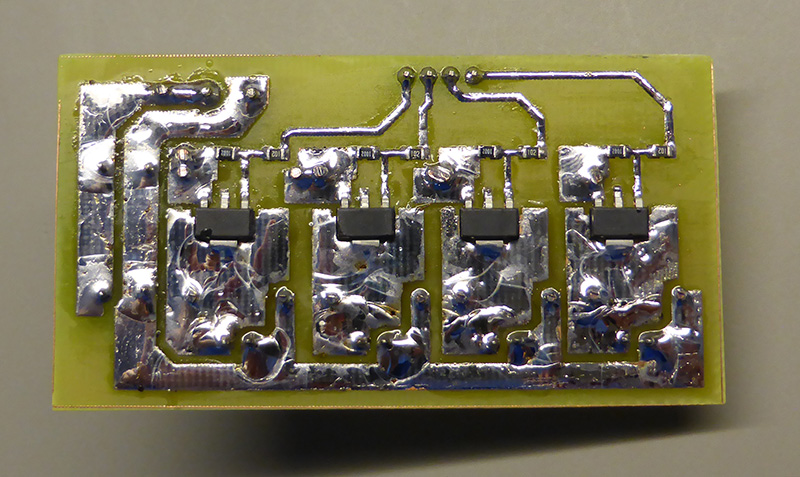
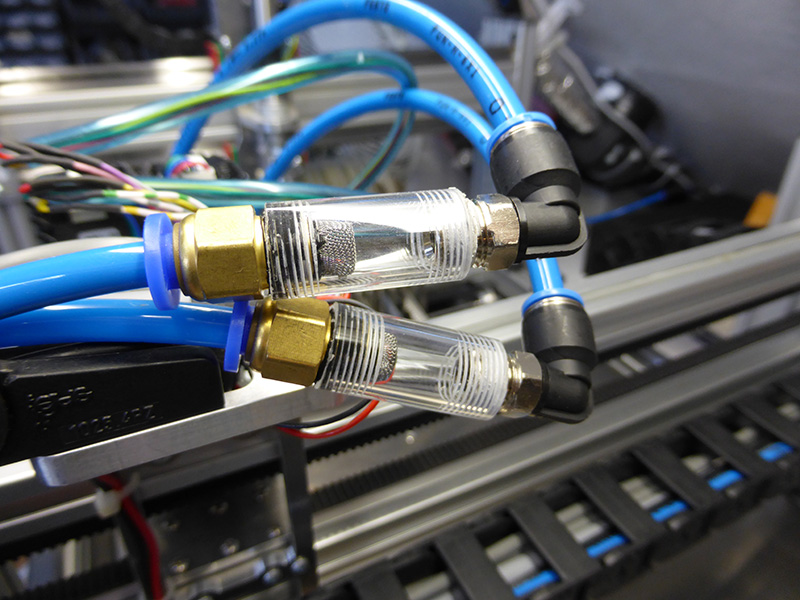
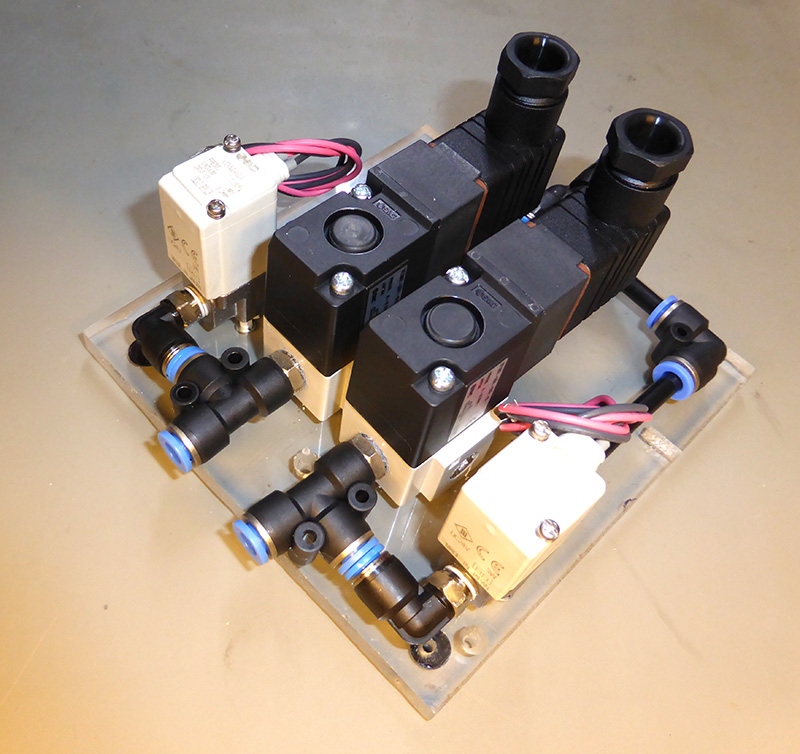
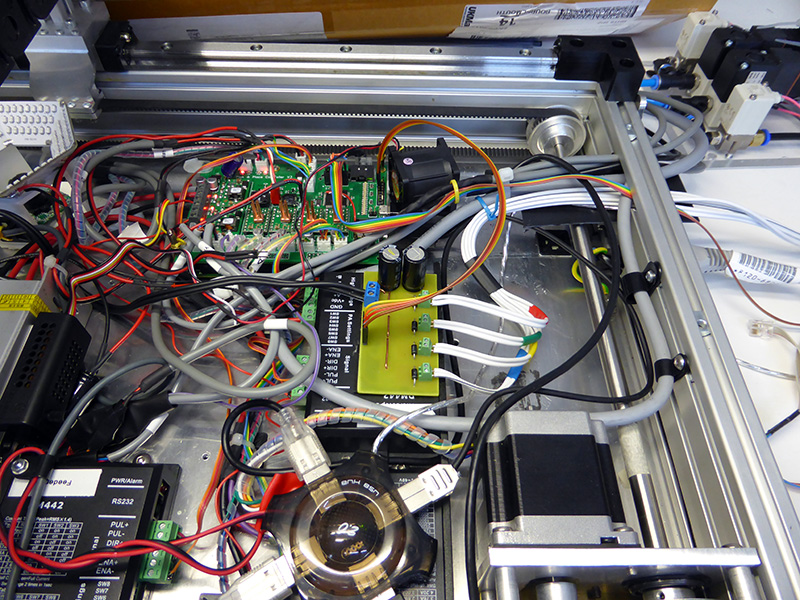
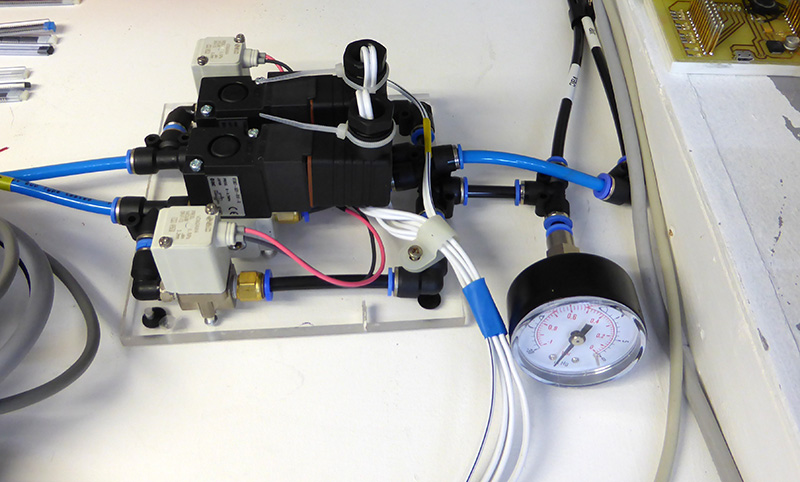
Connected to the air and vac supplies
Software Changes
In order for the new vacuum and compressed air solenoids to be controlled we had to change the pick and place software to perform the following commands when placing the components:
- Picker nozzle goes down
- Function setVAC2(bool inval) is triggered with “false” as the parameter
- Vacuum valve byte set to off
- Vac1AirPulse() or Vac2AirPulse() function is triggered which starts a new thread for the process
- Air valve byte set to on
- setIOPort() sends the commands to the controller board to turn off the vac and the air valve on
- Vac1AirPulseSub() or Vac2AirPulseSub() runs a loop with Thread.Sleep(10); to set a pause for the valves to change state and then once the time period has elapsed the air valve is closed.
- The picker nozzle goes up and continues with the next component.
The updated source code is available to download from github.com/briandorey/ModernUI-Pick-and-Place-Controller-Software/
We have now built over 200 boards with the new valve system and controller updates and the placement accuracy has improved and the suction at the nozzles is much stronger than before.
Future planned updates will be to adjust the timing settings for the control valves and stepper axis drivers to increase the speed of the placement.
Comments